
Arc Spray Equipment Metallisation Ltd
Arc Spray Engineering 563 followers 1mo Report this post Robotic Welding 🏗 We repair hundreds of tons of heavy engineering components annually, but we know there is a lot more going to scrap.
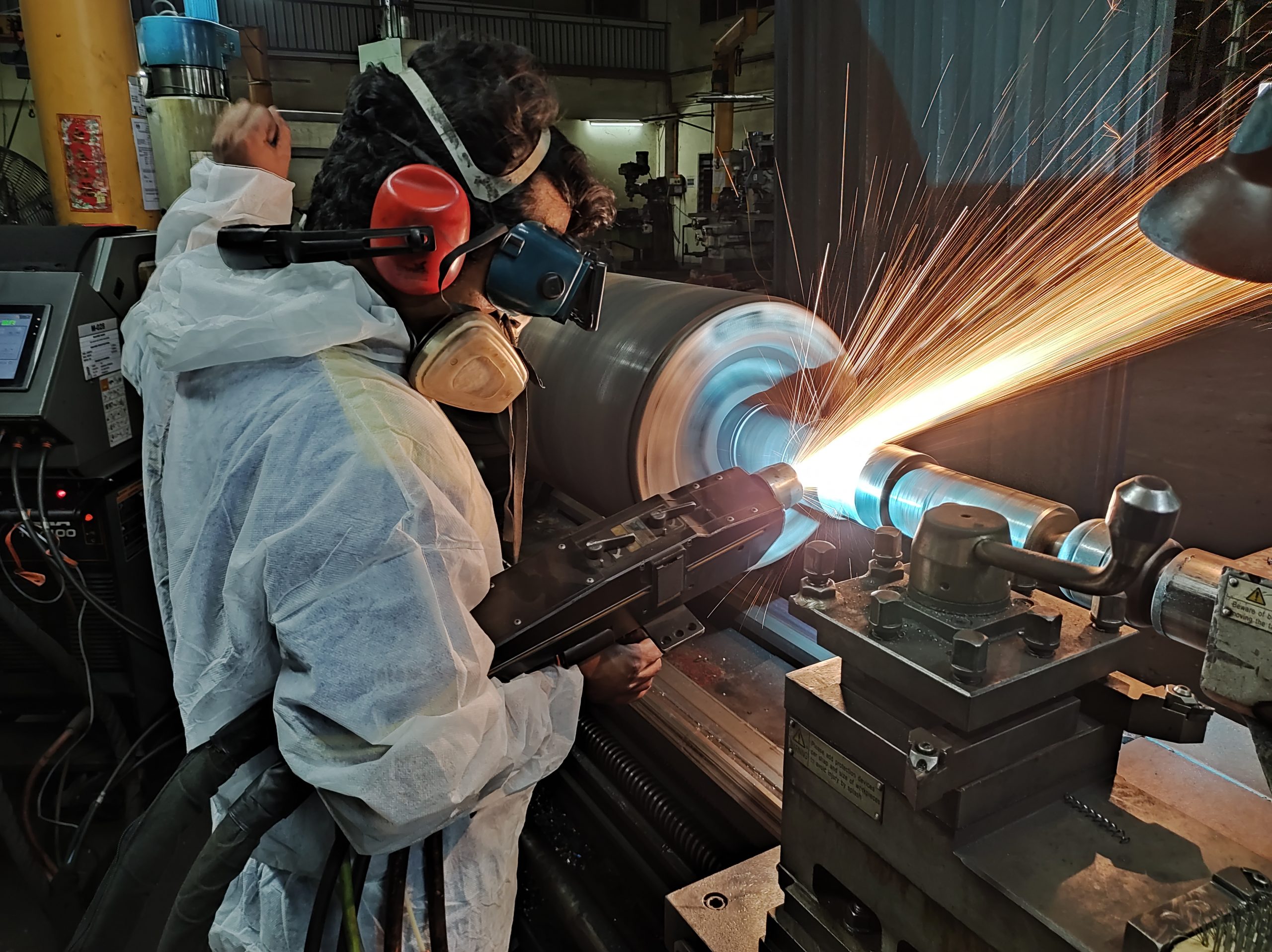
TCMARINE (M) SDN BHD » Thermal Arc Spray Repairing
Arc spray systems are commonly considered to be easy to operate and to automate and are offered as "push" or "push/pull" systems. A "push" system pushes the wire to the gun, is lighter and easier to use than a "push/pull" gun and is generally used for engineering applications which use hard engineering wires and have a shorter distance from the.

The Benefits of Arc Spray and HVOF Metallisation Ltd
The twin wire arc spray torch could also be mounted to an industrial articulated robot to automate the coating process. A wide variety of literature has focused on the TWAS process. The work from Hussary et al. (Ref ) focused on controlling power and temperature fluctuations in wire arc spraying systems.
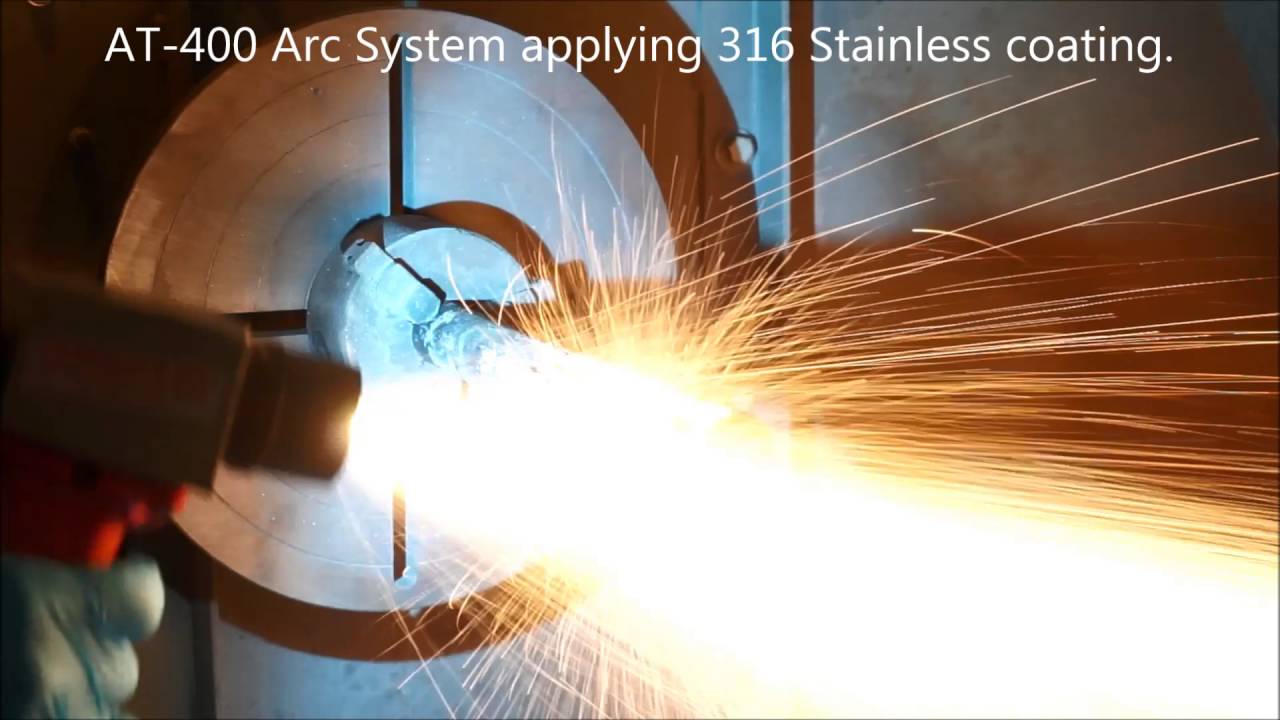
Wire Arc Spraying Stainless Steel Coating using AT400 Arc System YouTube
This presentation will show the basic research results of various automation targets such as rotating arc, magnetic arc oscillation, pipe welding and groove welding with acute groove angles. It will also show some examples of welding automation systems implemented in Korean industry such as ship building and automobile industries.
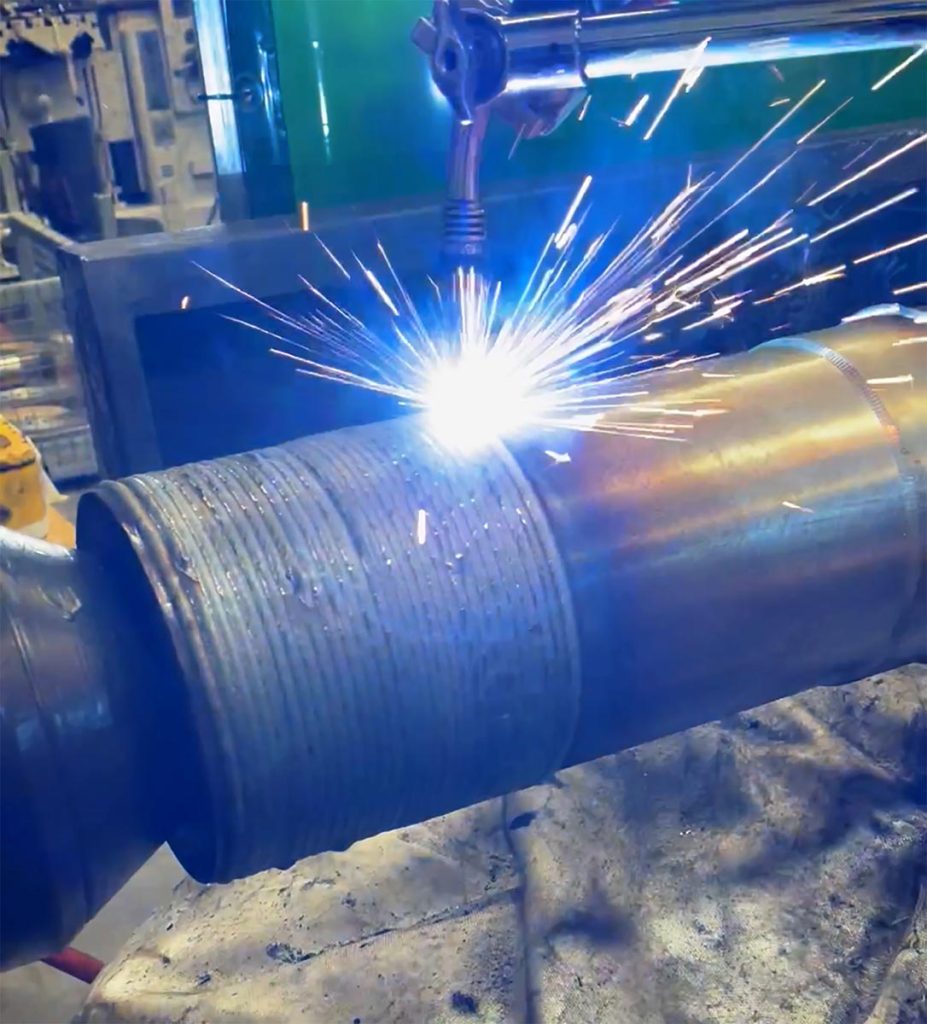
News & Insights Arc Spray Engineering
Arc spray is a thermal spraying process that uses an electric arc struck between two consumable feedstock wires to heat and melt the coating material. This molten material is then projected by a gas stream onto the target surface, where it instantly solidifies and bonds to the substrate.
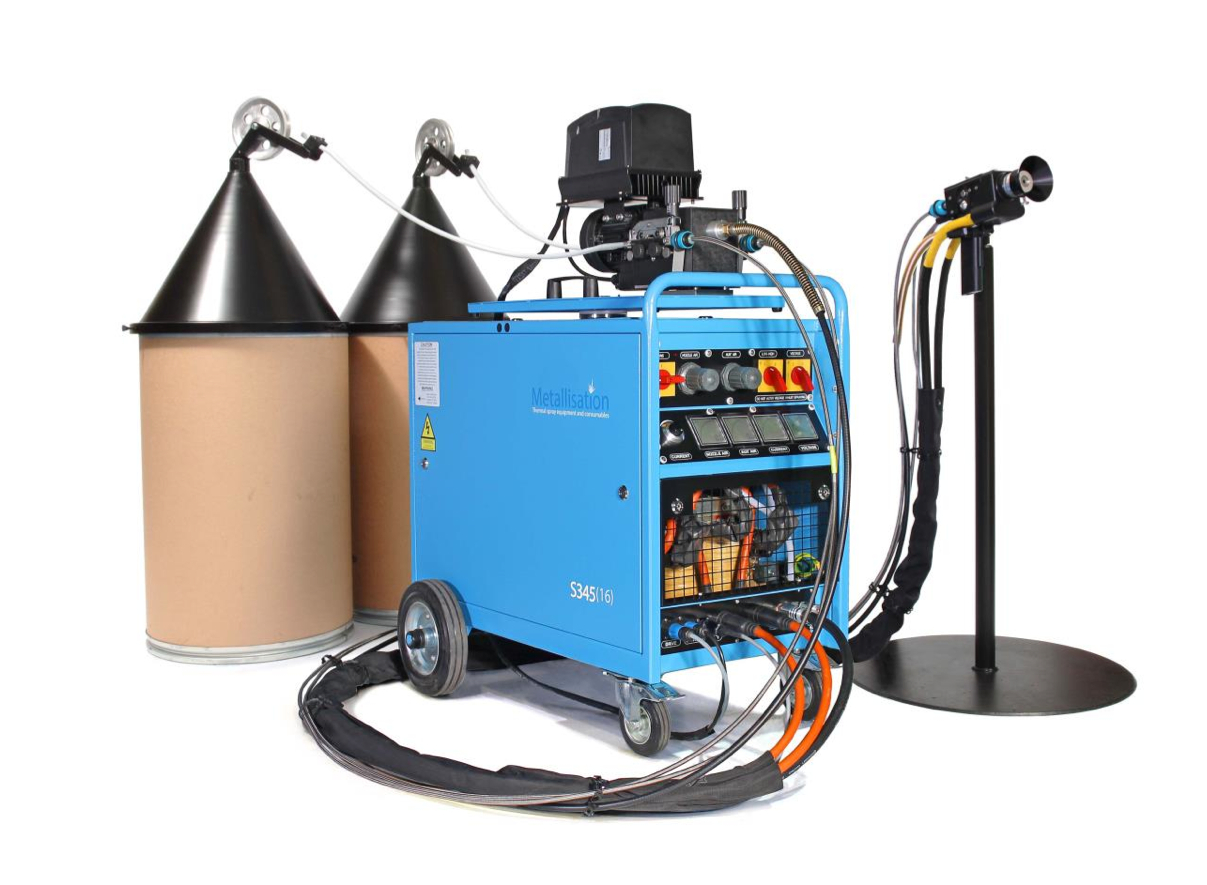
Arc Spray Equipment Metal Spray Suppliers NZ
Arc Spray (most often referred to as metalizing, TSA, TSZ, and TWAS) is the most productive and economical of all thermal spray coating systems. Arc Spray uses DC power to energize two conductive wires: one positive and the other negative. These energized wires are then fed through a feeder into a gun head.
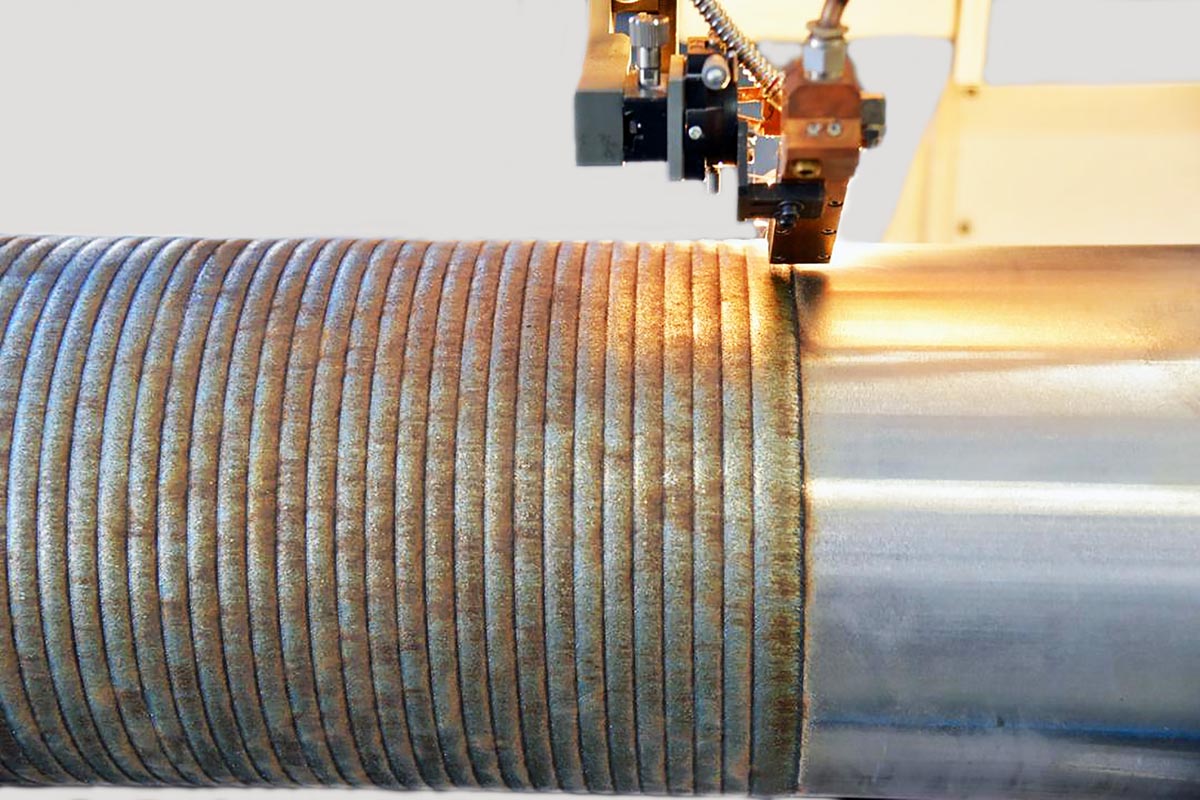
Arc Spray Engineering
In addition to high heat, the benefits of arc spraying include: † high feed rate of spraying; † the possibility of obtaining the coatings of high thickness, up to a few millimeters; † ease of implementation compared to other thermal spray processes (except flame spraying); † compatibility with the typical welding engineering;
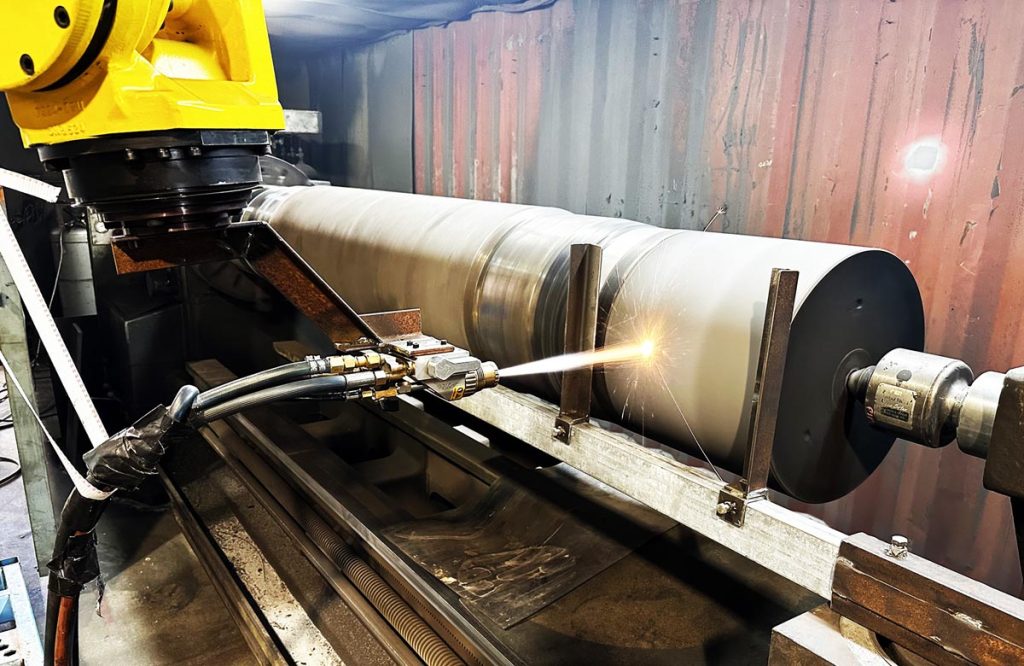
Arc Spray Engineering
Spray-arc transfer 'sprays' a stream of tiny molten droplets across the arc, from the electrode wire to the base metal. Spray-arc transfer uses relatively high voltage, wire-feed speed, and amperage values compared to short-circuit transfer. To achieve a true spray transfer, an argon-rich shielding gas must be used.

HORIZONTAL BORING Arc Spray Engineering
Arc welding is currently one of the most representative welding technologies in modern welding manufacturing, and is widely used in automobile processing, shipbuilding, and marine engineering [1], [2]. As shown in Fig. 1, arc welding has experienced several development stages. In the early stages, welding was manually conducted by welders, so.
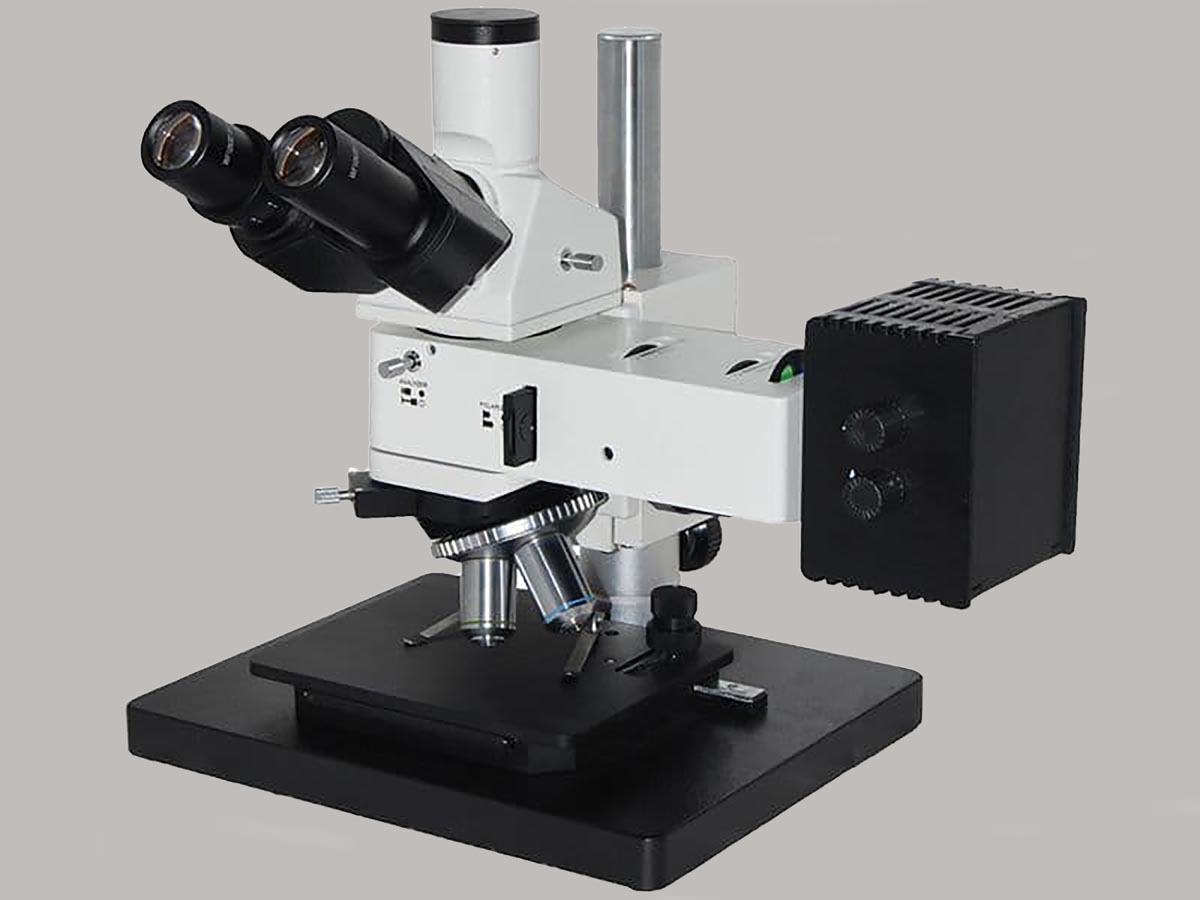
Arc Spray Engineering
Arc spraying has the highest deposition rate (15kg/h or above) of the thermal spraying processes and can be used to spray large areas or large numbers of components in repetitive production line applications. Arc sprayed coatings are most commonly used for corrosion protection or component reclamation.
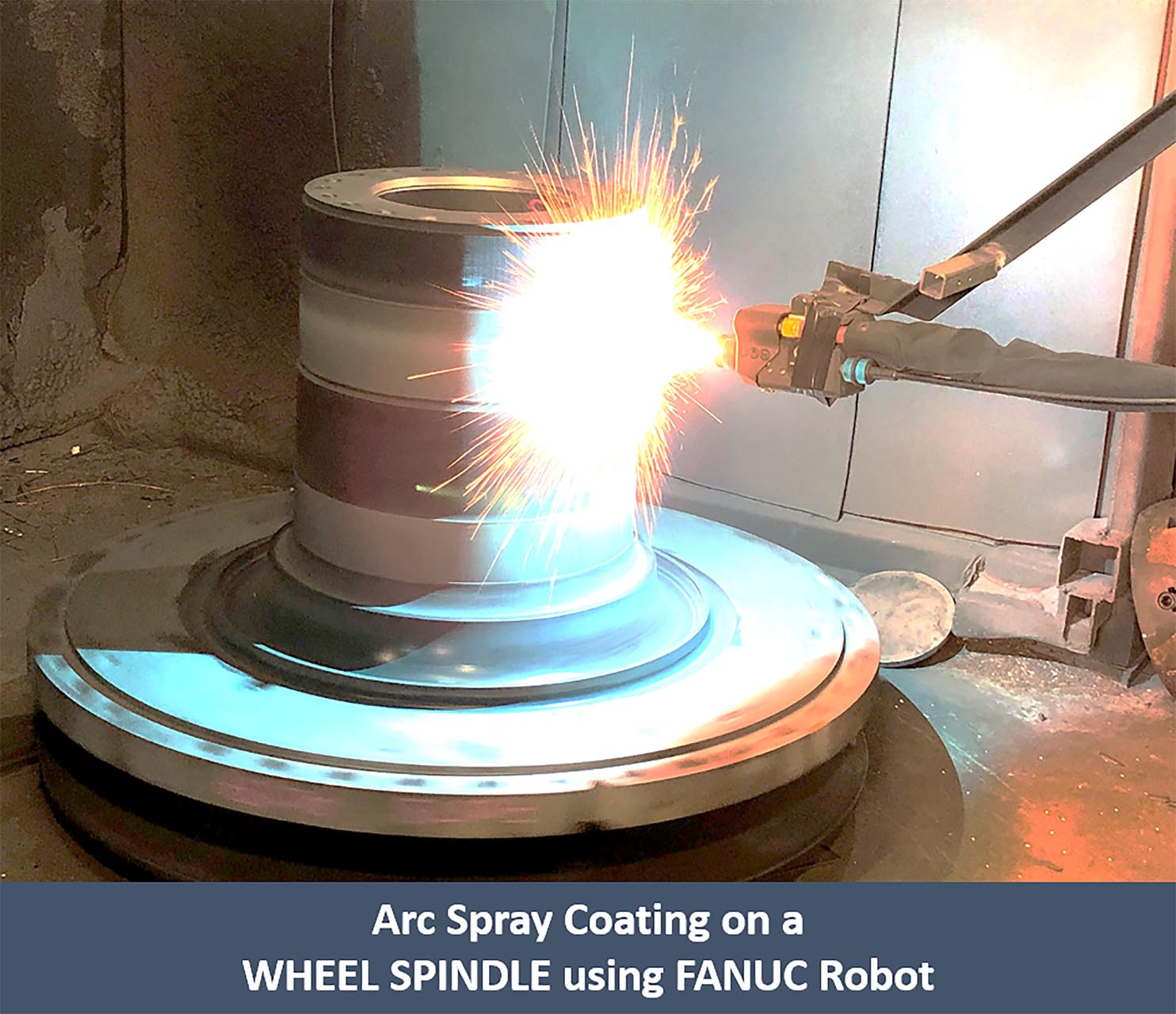
Arc Spraying Arc Spray Engineering
Industrial applications, however, were only possible after scientific research focused on fundamentals of this type of thermal spray process in the 1950s and 1960s [10-13].Arc spraying is very economical and therefore, has prevailed in many applications in spite of newly developed high-energy techniques such as plasma, detonation gun, and high-velocity flame spraying.

Conoce Qué Es El Proceso De Metalización Por Arc Spray
Figure 4 shows the three-level hierarchy of eight plasma spray parameters and their effect on coating properties. The first level shows the plasma spray parameters X i that control the second level temperatures of the plasma (X 1 to X 3), the particles (X 4 to X 6, X 8), and the substrate (X 7 and X 8). The third level constitutes particle.

Electric arc spraying (ENG) YouTube
Arc Spray Engineering Industrial Machinery Manufacturing Forrestdale, Western Australia 301 followers Follow View all 4 employees About us At Arc Spray Engineering we restore your components.

Cascading Arc Plasma Spray Technology Fabricating and Metalworking
The SE-TW 400 combines typical features of the arc spray technology, such as reliability and robustness, with the highest demands for process control and system compatibility of modern arc spray technology. The SETW 400 is designed to process all conductive wires relevant to thermal spray, solid wires and cored wires. New technology for the power […]

ARC SPRAYING METALLIZING SYSTEM L.B. Sidertech
Arc Spray Engineering. 182 likes. At Arc Spray Engineering we restore your components and equipment to their original condition. We ca
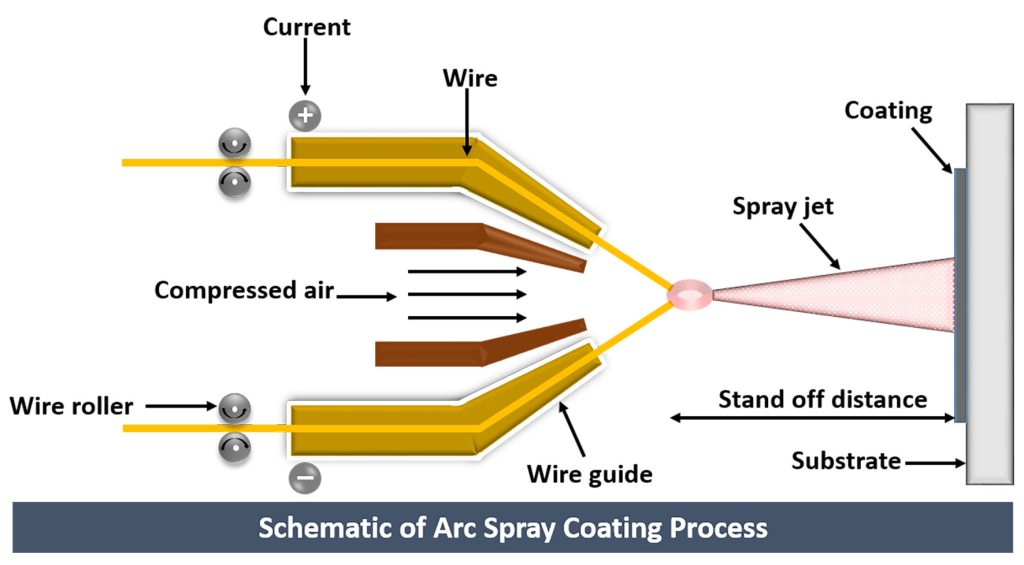
Arc Spraying Arc Spray Engineering
Most arc plasma systems are based on DC plasma technologies. However AC plasma systems can offer significant advantages versus DC plasma systems particularly in terms of efficiency, cost and reliability. They are also likely to overcome some of the limits of classical DC systems for some specific large scale high power applications. This paper presents a literature review of three-phase AC.